CLICK BELOW TO SEE A VIDEO OF OUR WELDER SEAL WELDING TUBES TO A TUBE SHEET
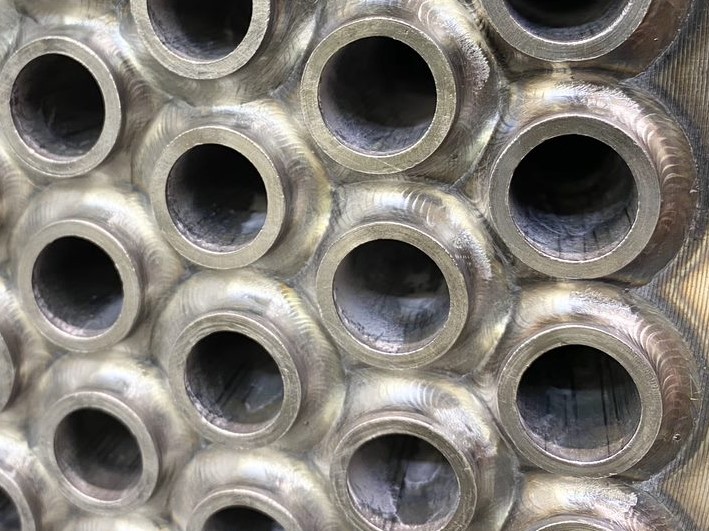
C H Murphy || Clark-Ullman, Inc has the capability to size, mechanically design, and fabricate your custom or standard shell and tube heat exchanger solution.
The primary function of the joint between the tube and the tube sheet of a shell and tube heat exchanger is to provide a seal between the tube side and the shell side. In many cases this is achieved by ‘rolling’ the tube. ‘Rolling’ tubes is the process of expanding the tube in the tube sheet tube hole to form a mechanical seal.
(Click here to see our previously published video showing the rolling of tubes)
If the operating environment is extreme, cleanliness is an issue, or the customer wants to step up to the next level of construction reliability, just ‘rolling’ a tube is not always sufficient. Customers have the option of ‘seal welding’ the tubes to the tube sheet in addition to the ‘rolling’ process. This provides a more robust design and offers another layer of leak protection between the tube side and shell side process streams.
At the top of this email is a video showing one our skilled welders seal welding a 18″ shell and tube heat exchanger.
Below is a sample drawing of a seal welded joint.
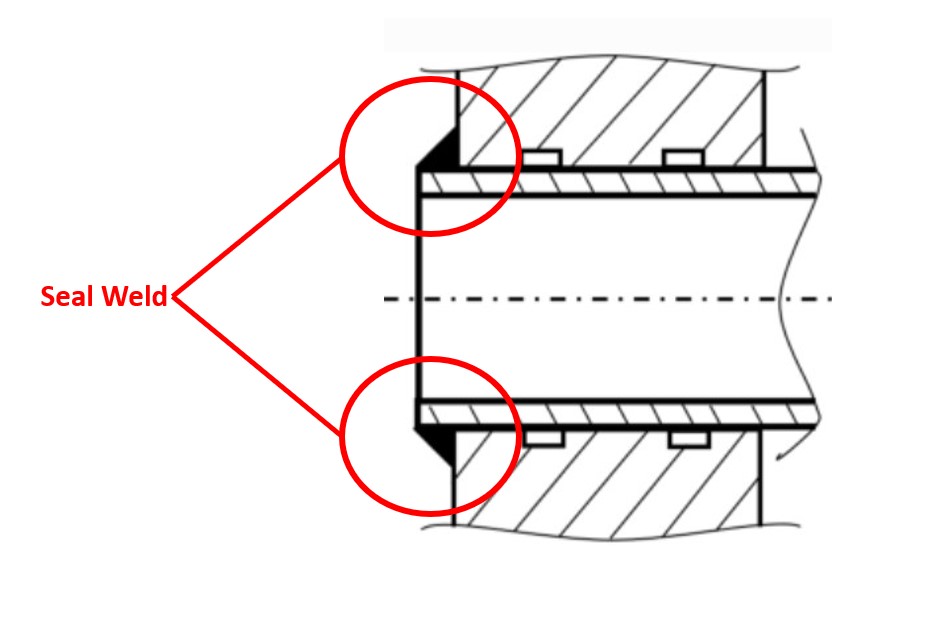
If you have any questions about seal welding or any other topic about shell and tube heat exchangers please give us a call.
C H Murphy || Clark-Ullman, Inc. has the capability to fabricate your heat exchanger in a range of sizes from bench top to large industrial units and in a range of alloys from carbon steel, stainless steel, nickel alloys and titanium.
See the pictures below of some of our projects!
Call us at 800.234.6255 to discuss how we can support your next project.
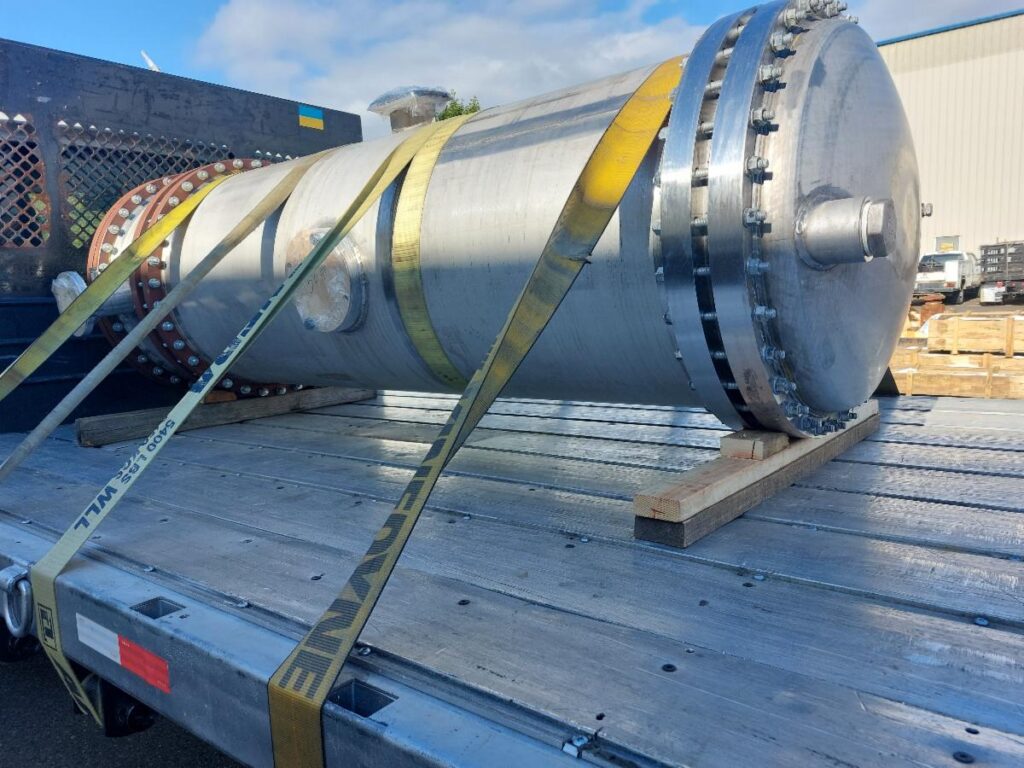
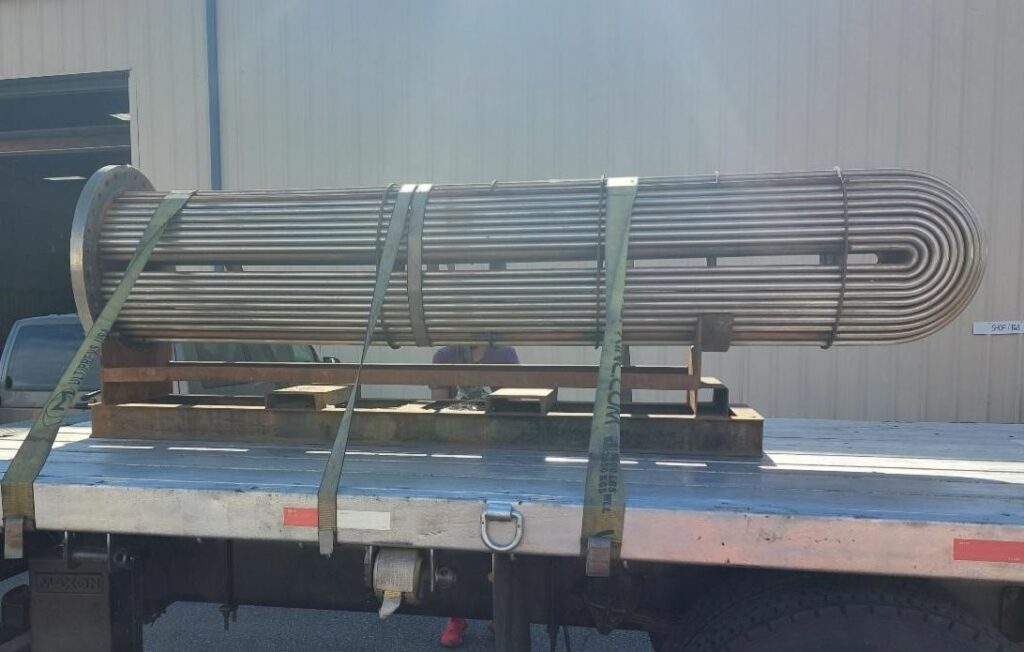
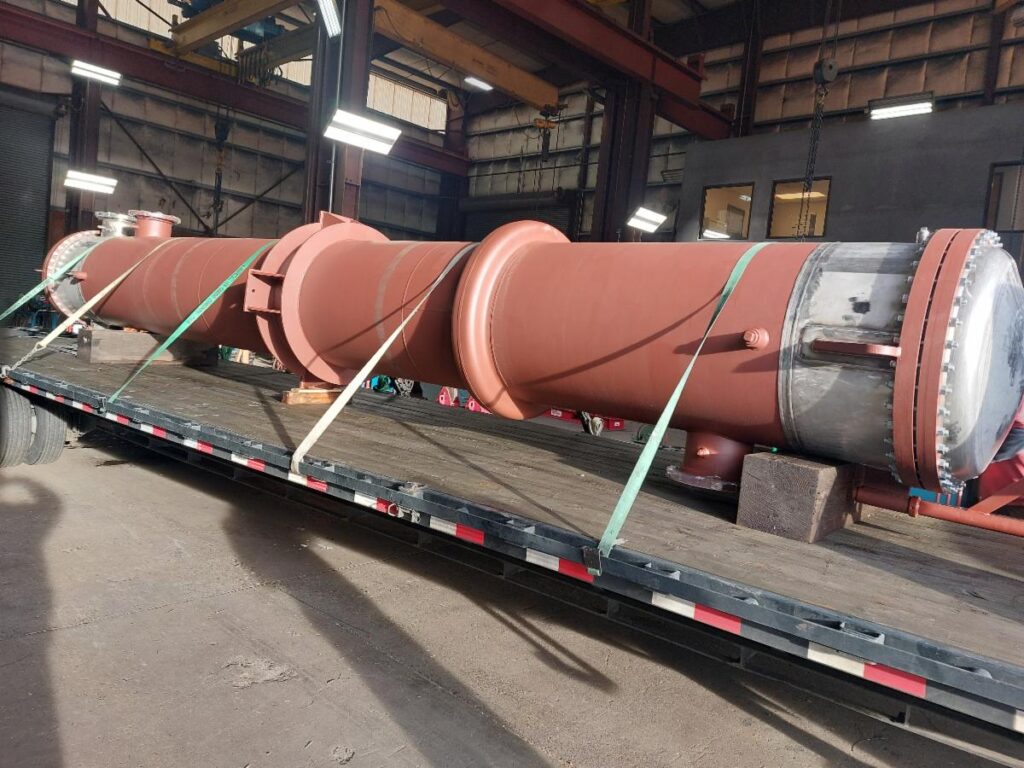
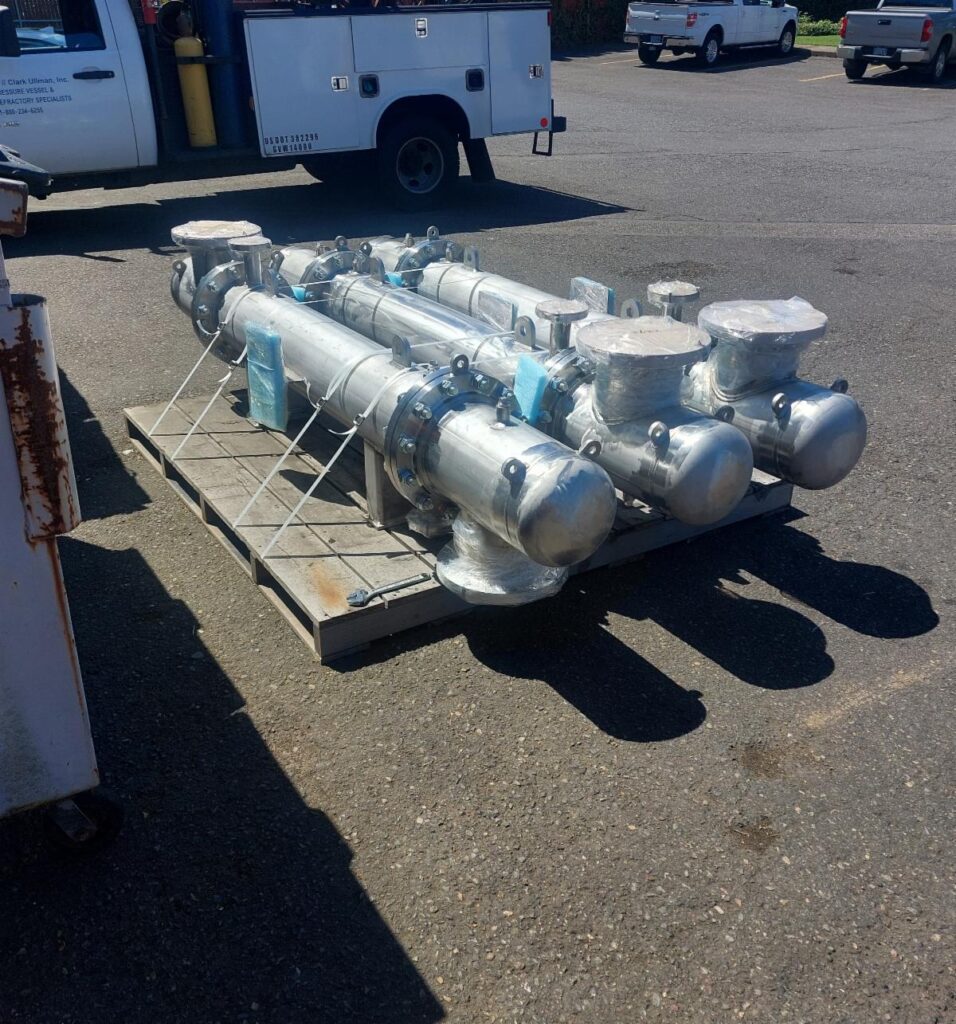
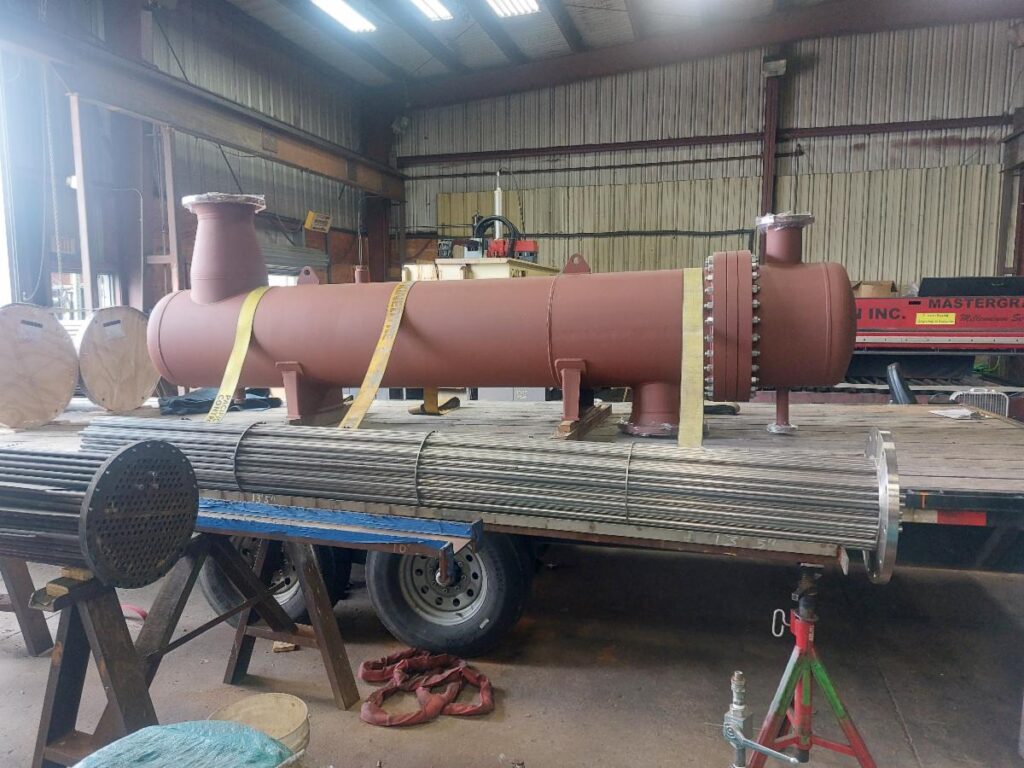
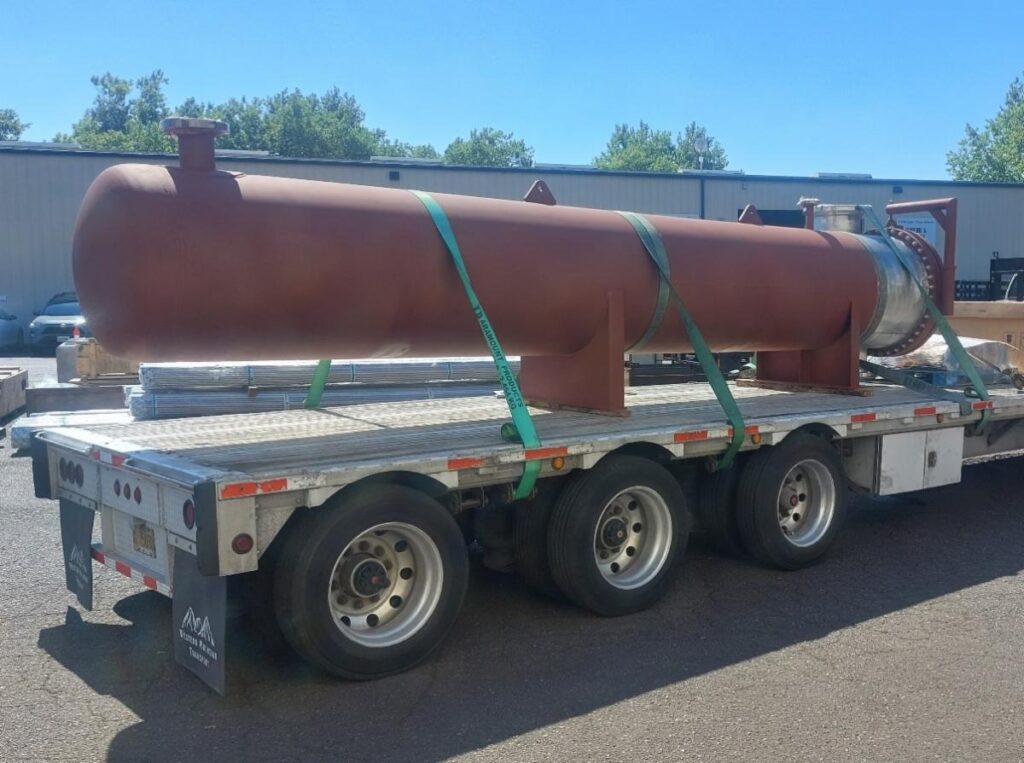
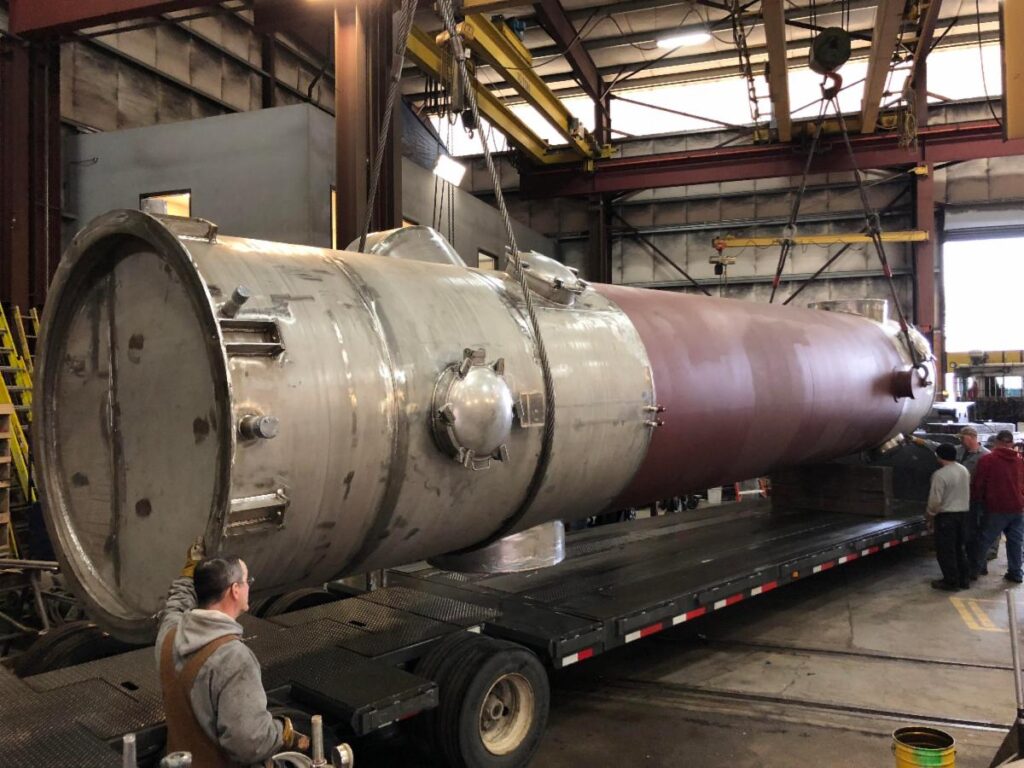
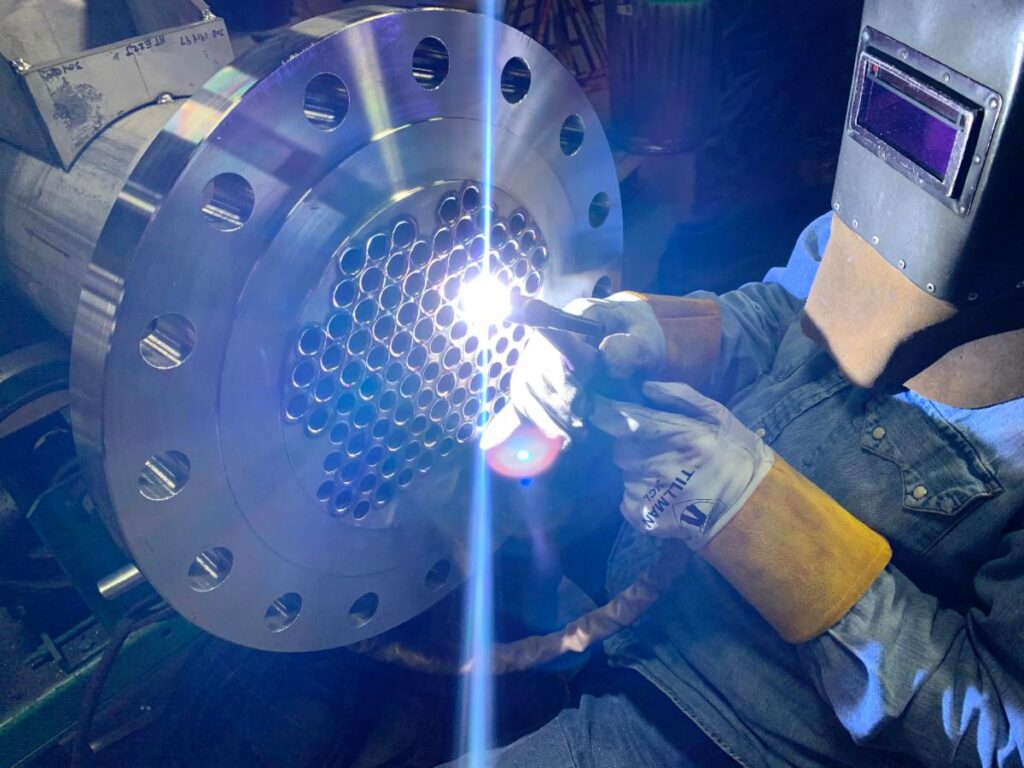